Introduction
Total Productive Maintenance (TPM) is a systematic approach to enhancing machine reliability and maintenance effectiveness. Companies worldwide have been leveraging TPM to reduce downtimes, improve production quality, and maximize asset utilization. However, like any other initiative, the real value of TPM is realized only when its success is measurable. The question arises: How does one track and measure the efficacy of a TPM initiative? Many leading TPM consultants emphasize the importance of Key Performance Indicators (KPIs) in this journey.
1. Overall Equipment Effectiveness (OEE)
Perhaps the most well-known metric related to TPM, OEE offers a comprehensive look at how effectively manufacturing equipment is utilized. OEE is calculated using three primary components: Availability (uptime vs. downtime), Performance (actual vs. ideal cycle time), and Quality (good products vs. defective products). A high OEE indicates that you’re producing quality products as fast as possible with minimal stop time.
2. Mean Time Between Failures (MTBF)
MTBF gives insights into the average time between equipment failures. A longer MTBF implies that the equipment is reliable and doesn’t fail often. Regular collaboration with TPM consultants can provide strategies to increase MTBF, enhancing machine reliability.
3. Mean Time To Repair (MTTR)
This metric measures the average time it takes to repair a machine after a failure. A shorter MTTR indicates that the maintenance team is efficient in diagnosing and fixing issues, ensuring that production can resume quickly.
4. Rate of Preventative Maintenance
One of the primary goals of TPM is to shift from reactive to proactive maintenance. This KPI measures how many of the maintenance activities are planned versus unplanned. A higher rate of preventative maintenance indicates a mature TPM environment.
5. First Pass Yield (FPY)
FPY measures the percentage of products that meet quality standards without needing rework or repair. A higher FPY indicates that the manufacturing process is stable and that the machines are well-maintained.
6. Employee Participation Rate in TPM Activities
TPM is not just about machines; it’s about the people who operate them. This KPI tracks the percentage of employees who are actively involved in TPM activities, such as daily maintenance checks, problem-solving teams, or TPM training sessions.
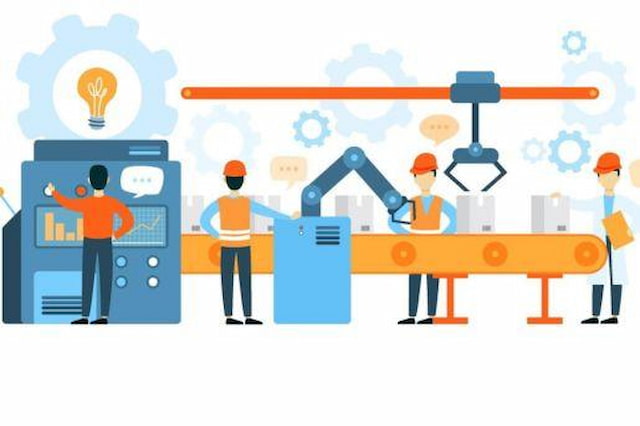
The Evolution of TPM and Its Relevance Today
The origins of Total Productive Maintenance (TPM) trace back to post-war Japan. Over the decades, it has evolved from being a basic tool maintenance strategy to a comprehensive approach that involves every level of an organization, emphasizing proactive and preventive techniques. This evolution makes understanding and measuring TPM more critical than ever. Leading TPM consultants often shed light on the holistic nature of this methodology and how its breadth has expanded over the years.
7. Total Maintenance System Efficiency
In line with OEE, which focuses on equipment efficiency, Total Maintenance System Efficiency (TMSE) looks at the efficiency of the maintenance system as a whole. This includes aspects like procurement of spares, inventory management, maintenance scheduling, and skills of the maintenance team. By optimizing the TMSE, organizations can ensure they have a robust support system for their equipment, minimizing potential downtimes.
8. Training Effectiveness Index
As TPM has grown in its scope, the importance of training cannot be stressed enough. The Training Effectiveness Index measures the efficacy of training programs in terms of the performance improvements seen post-training. An effective training program should not only impart knowledge but also translate to tangible on-ground improvements.
9. Safety Metrics
While the primary focus of TPM is maintenance and efficiency, it also considerably impacts safety. Metrics like accident frequency rate or near-miss incidents provide valuable insights into the safety culture of an organization. A decline in these metrics is a positive indication of the efficacy of the TPM program.
10. Cost Savings Through TPM
A key motive behind implementing TPM is to achieve cost savings. This can be derived from reduced machine downtime, improved efficiency, or reduced wastage. Tracking these savings gives a quantitative measure of the ROI from TPM activities, making it easier to justify further investments in this area.
Incorporating Industry 4.0 with TPM
With the advent of Industry 4.0 and its associated technologies, TPM is seeing another wave of transformation. The integration of smart sensors, predictive analytics, and advanced data tools has amplified the potential of TPM. Forward-thinking TPM consultants are now combining traditional TPM practices with these digital tools to provide an even more compelling value proposition.
For instance, predictive maintenance, powered by artificial intelligence, can forecast potential equipment failures before they occur. This means that instead of waiting for a breakdown or performing scheduled maintenance, companies can now perform maintenance activities just in time, further minimizing downtimes and associated costs.
The Human Element in TPM
While metrics and KPIs provide a quantitative way to measure TPM success, the qualitative aspects, especially the human element, cannot be ignored. TPM initiatives often require a cultural shift, a move from a reactive mindset to a proactive one. This involves not just training but also ensuring that employees at all levels are engaged and aligned with the TPM goals.
Success stories often emerge from shop floors where operators take pride in their equipment, treat them as their own, and are empowered to suggest and make improvements. Such an environment fosters innovation and continuous improvement, which are the bedrock of TPM.
The Role of TPM Consultants
Measuring TPM success is not a one-size-fits-all approach. Different organizations may prioritize different KPIs based on their unique challenges and objectives. This is where the expertise of TPM consultants becomes invaluable. They can guide companies in setting the right benchmarks, interpreting data, and evolving the KPIs as the organization matures in its TPM journey.
Conclusion
While TPM provides a robust framework for maintenance excellence, it’s the continuous measurement and analysis that truly drive its success. By diligently tracking the right KPIs, companies can ensure that they are moving in the right direction, optimizing resources, and realizing tangible benefits from their TPM initiatives.
If you are on the TPM journey or are contemplating starting it, consider engaging with experienced TPM consultants. They can provide a roadmap, set the right performance metrics, and ensure that your organization realizes the full potential of Total Productive Maintenance.